Dear user, the forum software has been updated. For the first login please reset your password.
Fusion 360 post processor headaches
First, I must state that I have spent hours researching this problem before finally deciding to register and post on this forum. I don't wish to upset anyone with a nagging problem that has previously been addressed. I have read every post related to my problem, but no real solution is available.
My machine is an S840 that I purchased last month. It is interfaced with the UC100 dongle device and controlled by the UCCNC software supplied with the purchase. It took me about one week of assembly time to completely build the kit. The assembly manual is not free of errors, I will confess. It is important to follow the Youtube videos for support
Before my purchase, I was expecting to use Fusion 360 as my CAD program of preference. As an electrical engineer, I rely on Fusion 360 for all projects assigned to me. In short, it is a fabulous piece of software for all professional engineers. I have used Fusion 360 for about one year to successfully generate the g-code to control my other CNC machine.
Sadly, though, Fusion 360 and its list of post processors are not enough to adequately control my Stepcraft 840 model. To date, the only piece that I have been able to machine is the Stepcraft logo provided as a sample file to test the machine following its construction. That file had been previously generated by some software other than Fusion 360. Aside from that first test job, my 840 has been useless. I have read about problems that other users have experienced. They are the same problems that trouble me, but I have made some painful progress, as a result of this forum. I thank those members who have posted their results under this section of the forum.
After building my CAD model in Fusion 360 and selecting Mach3 as the post processor, I load the g-code into UCCNC only to be surprised by a list of arc error alerts and a toolpath preview that is pitifully inaccurate. Another Stepcraft member posted a UCCNC processor that was provided by Autodesk for use in controlling a 4th axis. I tried that processor and the arc errors went away, but now I am left with a toolpath job that extends beyond the 840's Y-axis softlimits, according to the UCCNC warning. In the preview window, my model is, indeed, exaggerated in the Y direction with a ridiculously long toolpath travel.
At this point, I am out of further suggestions after exhausting my research efforts. I am really frustrated with my Stepcraft 840. It has not served me well and has only robbed me of valuable engineering time. I wish to be among the group of satisfied Stepcraft members who have achieved success with control of their machines via Fusion 360. There is even a professionally produced Youtube video with step-by-step instructions for machining carbon fiber material using Fusion 360 and a Stepcraft 840 machine--the exact same setup as mine.
Please pardon my plea for help with a problem that has been previously addressed on this forum. Can anybody provide a few tips?
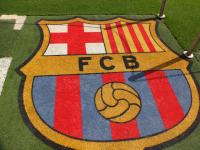
I'm not sure but there's sometime a discussion about this problem. I found one here:
Read especially the answer from "Kivinen". Hope it will help to give you new ideas how to solve the problem...
Viele Grüße
Hartmut
V2/420 China 800W wassergekühlt
UCCNC & ARDUINO ESTLCAM Controller
ESTLCAM & QCAD
-----------------------------------
DK5LH/G11
The G-code UCCNC accepts is documented in the UCCNCDocumentationUCCNC_usersmanual.pdf starting at page 40 (if using 1.0030 version of the software manual which came iwth the 1.2021 version of the UCCNC). Also the help tab in UCCNC has summary of G/M and other codes for g-code.
I have not used fusion 360, so I do not know exactly how it is done there, but in VCarve the post processors .pp stored in the ProgramDataVectricAspireV8.5PostP and those define different general parameters for the G-code, for example the units, how to substitute certain characters, what kind of line endings to use etc, and after that it has blocks what kind of G-code is generated for each operation (RAPID_MOVE, FIRST_FEED_MOVE etc).
By checking the autodesk forum post ( http://forums.autodesk.com/t5/computer-aided-machining-cam/post-processors-101/td-p/5916925) the post processors there are written in javascript, and some of those do have some parameters which can be tweaked.
I do not know if you can modify the post processors in the fusion 360 by just taking copy and putting it somewhere else and modifying the javascript but perhaps that is also possible.
I would first try to make very simple path in Fusion for example simple rectangle of 20 mm x 20 mm, and circle with diameter of 15 mm inside, then doing simple 1mm deep profile cut on line, and then saving the G-code in fusion and see what kind of output you get. Put both of those at center of material and use center point as the reference point.
It should be something like that (generated on vectric aspire using mach2/3 arcs mm post processor):
( Profile 1 ) ( File created: Wednesday July 27 2016 - 01:39 AM) ( for Mach2/3 from Vectric ) ( Material Size) ( X= 350.000, Y= 150.000, Z= 14.000) () (Toolpaths used in this file:) (Profile 1) (Tools used in this file: ) (0 = End Mill {3 mm} 2-Flute Fish downcut) N100G00G21G17G90G40G49G80 N110G71G91.1 N120T0M06 N130 (End Mill {3 mm} 2-Flute Fish downcut) N140G00G43Z20.000H0 N150S18000M03 N160(Toolpath:- Profile 1) N170() N180G94 N190X0.000Y0.000F1400.0 N200G00X0.000Y7.500Z3.000 N210G1Z-1.000F1200.0 N220G3X-7.500Y0.000I0.000J-7.500F1400.0 N230G3X0.000Y-7.500I7.500J0.000 N240G3X7.500Y0.000I0.000J7.500 N250G3X0.000Y7.500I-7.500J0.000 N260G00Z3.000 N270G00X-10.000Y10.000 N280G1Z-1.000F1200.0 N290G1X10.000F1400.0 N300G1Y-10.000 N310G1X-10.000 N320G1Y10.000 N330G00Z3.000 N340G00Z20.000 N350G00X0.000Y0.000 N360M09 N370M30 %
The text in parenthesis are coments, the Nxxx is line numbers. N100-190 are initialization, changing tool 0 (T0M06), setting spindle speed (S18000), starting spindle (M03), setting Feed rate (F1400). These lines can cause issues if there is something like home location, or safe location that is outside the usable range of stepcraft, or if there is some other G-codes which might cause issues. Checking those G-codes outputted by your post process against UCCNC manual, might help.
After that starts the program on line N200. Line N200 moves (G00) to start of circle (X0.000 Y7.500 Z3.00 (my safe height is 3mm, and reference is on top of material)), line N210 plunges 1mm in to the material (G1 Z-1.000), then N220-250 makes the circle using CCW arc interpolation. Line N260 lifts tool up, N270 moves it to start of rectangle, and N280 plunges it down, and again N290-N320 draws the rectangle, and N330 lifts tool up, N340 and N350 moves it to the parking location (X0, Y0, Z20). N360 turns mist/coolant off (M09) and N370 terminates program (M30).
Important thing to check is that units in g-code should be mm, i.e. the rectangle should be X10/-10 and Y10/-10 as the rectangle was 10mm (and centered around zero location).
If you check the generated g-code and check how it differs from the above, you might find clues what is wrong with the post processor in the fusion 360.
Stepcraft 2 840 Kickstarter make anything package
HF500, 3D print, Drag Knife, etc
UCCNC + UC100, V-Carve

Hi,
I've just ordered a Stepcraft system and intend to use Fusion 360 combined with UCCNC or Mach3. I'm leaning towards purchasing UCCNC since there seems to be some indications that it performs better (but please feel free to object if I've gotten it wrong). A friend of mine is successfully using Fusion together with Mach3. However, the tool length sensor only works with UCCNC according to the Stepcraft crew, which is why I hope to be able to use UCCNC instead.
I'm therefore very curious to hear if you've solved your problem since I anticipate that I will run into exactly the same problem when my system arrives in a few weeks.
Warmly,
Per Takman
Sounds like you are not setting up your origin in fusion360 cam correctly before making operation. If you read your g code, and see numbers that are out of bounds, then this is the cause. The 4th axis fusion file is great !.
If the g code looks correct, then the problem is coming from an initial move that creates incorrect offsets for the operation. It's one or the other.
Sounds like you are not setting up your origin in fusion360 cam correctly before making operation. If you read your g code, and see numbers that are out of bounds, then this is the cause. The 4th axis fusion file is great !.
If the g code looks correct, then the problem is coming from an initial move that creates incorrect offsets for the operation. It's one or the other.
Would someone who is successful using Fusion with a stepcraft be so kind to post a video of setting up a CAM operation on a basic 2D part, post processing and importing to UCCNC? Thanks
Short news:
In a few weeks there will be a postprocessor available espacially for the Steppi, keep patient...
Produktevangelist 🙂
Es grüßt mit der Ihm gegebenen Freundlichkeit...
...der Thomas
I did not use Fusion 360 yet, but thinking of trying it soon and wanted to ask what is the problem with running Fusion 360 with UCCNC?
As far as I know UCCNC is code compatible with Mach3, so isn't there a Mach3 post processor for Fusion 360 which we can use with the UCCNC?
checkout my other post, it has the POST for stepcraft attached
Nick
Hi Sir did you solved the problem?
I am facing the same problem now.when I load the G code file generated by Ultimaker Cura the STL file created by Fusion360. There is a long tool path on y axis in UCCNC's tool path display but I can't see the G code. I have attached the Screen shots here please help me to solve it if you can.
Kind Regards
Suresh.G
Hi any body help me,
I have a problem when I load the G code file generated by Ultimaker Cura the STL file created by Fusion360. There is a long tool path on y axis in UCCNC's tool path display but I can't see the G code command for the move on the G code file. I have attached the Screen shots and the G code file here please help me to solve it if you can.
Kind Regards
Suresh.G

Hi,
I've just ordered a Stepcraft system and intend to use Fusion 360 combined with UCCNC or Mach3. I'm leaning towards purchasing UCCNC since there seems to be some indications that it performs better (but please feel free to object if I've gotten it wrong). A friend of mine is successfully using Fusion together with Mach3. However, the tool length sensor only works with UCCNC according to the Stepcraft crew, which is why I hope to be able to use UCCNC instead.
I'm therefore very curious to hear if you've solved your problem since I anticipate that I will run into exactly the same problem when my system arrives in a few weeks.
Warmly,
Per Takman
Dear Per,
I am using the tool length sensor together with Mach3 on my Stepcraft SC420/2 without any issue. There is some code you have to write for the tool length sensor and everything will be fine.
If you need it, I can give you the code.
Best regards,
Ronald
The only difference between man and boys is the price of their toys.
------------------------------------------------------------------------------------
Fusion360, Mach3, UC100, SC 2/420, Kress 1050 FME-P, Sorotec Nutenplatte, Sorotec Vakuumtisch
- 44 Foren
- 7,338 Themen
- 63.2 K Beiträge
- 10 Online
- 26.3 K Mitglieder