Dear user, the forum software has been updated. For the first login please reset your password.
Accessories for a PCB milling setup
Hello everybody,
I am looking for a complete setup for a machine that I would like to use mostly for PCB milling.
I will pick a model between V2/210 and V2/300 because I dont need a huge workspace. About the other choices:
- interface: given that my workflow will be Eagle->gcode->machine, do you suggest to pick the UCCNC interface?
- spindle motor: is there a motor included with the fully assembled machine? if no, which one do you suggest for PCB milling? is a Dremer enough?
- other mandatory parts: are there other mandatory components that I need to purchase?
- other optional parts: are there any optional components that I should consider for possible future upgrades?
I don't have experience with this kind of machine so I having some difficulties to figure out which is the minimal setup that I need to have fully working PCB milling machine.
Thanks in advance!
Hi Khepri,
I've used my V2/420 for pcb engraving/milling, and like you I have chosen the Eagle - pcb_gcode.ulp route.
UCCNC/UC100 does all that is required to run the GCODE without requiring any editing once the ULP parameters are correctly set. If your budget will stretch to it go for an HF500 - this can be controlled by the generated GCODE so that the spindle is started and stopped automatically for tool changes. The ER11 collet system is widely used and low cost - tools are readily available to fit - 3mm does for most things.
You will definitely need a flat milled sacrificial layer under the pcb laminate - this will need to be flat and level to better than .05mm for fine tracks to be accurately cut. I use a carbide 30 degree cutter and a depth setting of around 0.25mm. Z - axis zeroing is critical, and at the moment I use an electrical contact between cutter and the copper to set mine - probably to better than .01/.02 mm.
Holding the FR4 in contact with the sacrificial layer is vital to final track accuracy, and to this end I made a small vacuum table and bought a low cost vane type vacuum pump to supply it. Using a shop vacuum is risky because of lack of motor cooling (fire risk) if the system is properly sealed. Another approach is to use double sided tape of course.
At the moment I am building a tool length sensor to automate zeroing the Z-axis to better than .01mm. Repeatability is critical, so I am replicating the 6 ball touch sensor in my design rather than use a microswitch to sense the position. It is very difficult to source a microswitch which even mentions repeatability in its specification, hence the DIY approach.
To date I have used only through hole components and 0.1" IC's, but I intend to try to use some of the bigger SMD IC's in future designs. Routing tracks between 0.1" IC pins is no problem once the machine backlash is properly compensated - this is vital!.
Nuff said for now!!
Peter
SC 420/2, Industrial VFD spindle from StoneyCNC
UC100 + UCCNC
Cut2D, Autosketch10, Draftsight, Eagle 9.5.1
There is no problem, however simple, that cannot be made more complicated by thinking about it.

Buy the StepCraft just with a parallel interface and buy EstlCam and make the Arduino Setup.
With this setup you can even measure the height of the PCB on different points on the surface to level it correct.
In addition, this is by far cheaper than UCCnc.
The price for EstlCam is 49€ and an Arduino UnoR3 is somewhere at 10€
You can get informations abt. EstlCam here: EstlCam
MfG
Roy
SC 600/2; SolidWorks; UCCnC und UC100; EstlCam und Arduino Steuerung; KRESS 800kfme;
FR4 pcb material is never totally flat, so measuring its Z profile is no guarantee that it will not flex when a tool is applied. Found that out the hard way!! For good accurate milling, the board must be rock solid.
Remember that the Uno will need to be housed, powered, connected and programmed.
Accurate backlash compensation is vital to success.
One of my first simple pcb efforts.
SC 420/2, Industrial VFD spindle from StoneyCNC
UC100 + UCCNC
Cut2D, Autosketch10, Draftsight, Eagle 9.5.1
There is no problem, however simple, that cannot be made more complicated by thinking about it.

Hi,
the bending of the PCB can be prevented by simple double side adhesive tape or better by a vaccum pad.
Some people also use spray glue.
The housing of the arduino is needed or not, but I would recomment to house it. But we talk abt 2€ or if you whish I print one for you.
Programming of the Arduino is done by EstlCam with just a mouse click. No big issue.
The Arduino is powerd by the USB Cable from your computer, there is nothing else needed.
This is really an easy and cheap solution. The money you safe, you can spend in a vaccum pad.
I run mine (and I am not the only one) with a standard vacuum cleaner.
The functions you have in EstlCam are by far better than UCCnc. (I have both by the way, and if you like, you can buy my license and also the UC100 USB Adapter)
The CAM Module of UCCnc is useless in my opininion, but maybe you don't need it for your set-up.
I forgot to mention: I am not related in any way to the programmer of EstlCam! I am just extremely satisfied.
MfG
Roy
SC 600/2; SolidWorks; UCCnC und UC100; EstlCam und Arduino Steuerung; KRESS 800kfme;
Don't hesitate to get the UC100 + UCCNC, it is a very good and easy to use control.
The newest release have PCB leveling function built in, so you can level your PCB on the table with probing.
If it were me I would take up DerRoy's offer of his UCCNC + UC100 - at a good second hand discounted price 👿
This route has proven very straight forward for me - knowing I can go straight from Eagle .brd via the ULP to milling the board is a big plus. No editing required!!
SC 420/2, Industrial VFD spindle from StoneyCNC
UC100 + UCCNC
Cut2D, Autosketch10, Draftsight, Eagle 9.5.1
There is no problem, however simple, that cannot be made more complicated by thinking about it.
I don't want to be a jerk with buying this off the OPs hands, but if DerRoy offering them for a good enough price then I would be interested to take it.

Hi,
as I mentioned, I am willing to sell this.
But so far I have never been thinking abt. a price.
You can make an offer, but I think we should handle this in PN and not in this thread.
MfG
Roy
SC 600/2; SolidWorks; UCCnC und UC100; EstlCam und Arduino Steuerung; KRESS 800kfme;
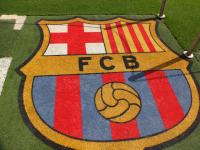
As an alternative to EAGLE I'm using Target3001!
The output of this software can directly be also a G-Code file. The small version of this SW is free and ok for 2 layers and as I remember 250 Pins.
Unfortunately all my material is bended. So I need always a prior surface leveling. This feature is implemented in ESTLCAM if using the ESLCAM Arduino controller or in the latest version of UCCNC (look at "CNCDRIVE" for download). But also there is an separate macro available for UCCNC which does this.
Here I placed a post regarding this thematic: Auto-leveling
When using surface leveling before PCB milling it can be done very precise. I was able to perform PCB milling with a 30° engraver milling the copper with Z= 0,06mm , so just milling the copper, not the basis material.
Viele Grüße
Hartmut
V2/420 China 800W wassergekühlt
UCCNC & ARDUINO ESTLCAM Controller
ESTLCAM & QCAD
-----------------------------------
DK5LH/G11
I am not much aware of the PCB milling but still as per my research to your configuration I recommend you to try this configuration, 331x305x120mm (X, Y, Z) for your PCB milling. No doubt it is not what you exactly want but I think it suits you because it has higher efficiency than that one.

Guess you are up to 9 months late with your recommendation. 🙂
SC 420 mit DIY parallel + Proxxon mit Mod + HF500 + SprintLayout + LibreCAD/QCAD + FreeCAD +WinPC starter/USB->EstlCAM + EstlCAM LPTAdapter + EstlCAM Handrad + DIY Vakuumtisch
Gruß, Andreas
Hi...as per my knowledge you need a flat milled sacrificial layer under the pcb laminate - this will need to be flat and level to better than .05mm for fine tracks to be accurately cut. I use a carbide 30 degree cutter and a depth setting of around 0.25mm. Z - axis zeroing is critical, and at the moment.
Hi,
Having a flat, machined sacrificial base is clearly essential for any pcb milling operation to be successful, but equally important is to ensure that the workpiece is flat too,
If there are any gaps between baseplate and the underside of the workpiece (FR4??), then the springiness of the workpiece will distort the programmed widths of tracks and isolation.
Ideally a vacuum hold down should be used, but maybe double sided tape is acceptable if the problem of adhesive on drills when holes are drilled can be overcome. Personally I use a simple homemade vacuum table and have some excellent results. Look at some of my earlier posts on the subject.
Peter
SC 420/2, Industrial VFD spindle from StoneyCNC
UC100 + UCCNC
Cut2D, Autosketch10, Draftsight, Eagle 9.5.1
There is no problem, however simple, that cannot be made more complicated by thinking about it.
- 44 Foren
- 7,336 Themen
- 63.2 K Beiträge
- 3 Online
- 26.3 K Mitglieder