Dear user, the forum software has been updated. For the first login please reset your password.
D SHAPED TUBE MILLING
Hi Guys,
I'm trying to make a D shape tube out of pine or hardwood, and would like to get some advice from the experts and home users on what you think may work best.
The Tube Dimensions are approximately 70x70mm with a D on one of side approximately 30 high ( Total witch approx 100 incliding D ) and tubelength 700 - 800mm.
I have the Stepcraft2 840, and 4th Axis Circular chuck / laithe setup, with Vetric and Fusion360 software.
What I imagined doing, was getting a solid piece of wood, maybe 100x100x800, placing it on the circular chuck (raised off the table so that it rotates clearly), and then End Milling a side flat, rotating the chuck 90 degrees, repeating x 2, and then doing the curved top last with a 6mm end mill for roughing, then the 3 or 1mm to finish the D curve off.
Is it possible to use the Vetric software or Fuision 360, to write a toolpath that will wo this automatically, or do I have to write 4 separate tool paths and manually rotate the chuck 90 degrees ?
I am using a 3D file and then importing that into the material workspace to generate the tube shape.
..
Plan B, was to not use the rotatry axis, and instead just lay the block on the plate, Flatten 2 sides, then align the flattened 2 sides to flatten the bottom of the tube at 90 degrees, then place the tube with D facing upright, and rough and flatten the top. Obviously there is a lot more room for error in this as it relies on many piece modifications, instead of the rotary axis rotating
What do guys think ?

Hi finch,
Long story short: A picture/drawing/screen-shot would tell us more than thousand words ... 😉
If you have already something to show us please post it and I'm pretty sure somebody can help you with the right work-flow.
It's not only about tools it's also about skills! 😉
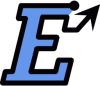
Hi,
this part is quite simple to manufacture without the 4th axis:
- Draw it with a CAD Program and save as STL file...
- Open the file with Estlcam, limit depth to the height of the rounded area and create the CNC program...
- Make a rectangular blank with exact width and height - but longer than required...
- Clamp it at its ends (this is why it should be longer), machine it and finally cut the ends off...
- You can alternatively also cut from solid stock without cutting a blank first - but this will take much longer to machine and requires a very long tool...
Short introduction about 3d milling with Estlcam:
https://www.youtube.com/watch?v=xw0ZFf75lAM
Christian
Ok - thanks, yeah we ran into all kinds of problems, trying to get this done.
The first one being this whole model assembly is too close the the Z axis limit switch - running the thick aluminium clamping table with a 6mm bit - we only had about 95-100mm Z height maximum from top of aluminium base plate to the bottom of 6mm face mill, to mill an 87-88mm block of wood - we were lucky, as I thought the wood was actually 100x100
Has anyone looked into modifying the Spindle holding arm to raise the spindel height to allow larger facing operations? Looks like I could get another 30mm Z height and still clear the arm ?
Also - I wanted to use the rotary axis to avoid all this multiple tool file, rotating parts - refixing them etccc, but the Z height is prohibitive and will not allow this to happen. If I can modify the Spindle higher, then I may be able to get full use of the rotary axis. Thoughts?

Has anyone looked into modifying the Spindle holding arm to raise the spindel height to allow larger facing operations? Looks like I could get another 30mm Z height and still clear the arm ?
Hi, check this out: DIY Spindle Adapter (Sorry, only in German available ...)
Question: For what is this "D shaped tube"? Do you really need to process this in one piece? Whats about to process it in two pieces, a bottom and a top one, put it together, done ...
It's not only about tools it's also about skills! 😉
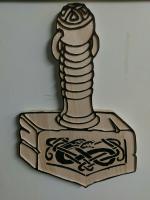
I bought even a radius cutter.
( http://www.destockoutils.fr/coffret-alu-15-fraises-carbure-varo,fr,4,28380.cfm)
The rounded corners on the first side, and then the workpiece flipped to process the second side.
That goes well with wood.
Material: Pine 28mm x 60mm
Wenn du heute nur das tust - was du gestern schon getan hast - dann bleibst du auch morgen nur da - wo du heute schon bist
Rüdiger
☺☺☺ Lass mal späne produzieren!!! ☺☺☺
Pro Vario 10-05 D200 / Estlcam / WinPcNc USB / Kress 800
vorher: 600er / Estlcam / Mach3 UC100 mit USB Anschluss,HF500
That spindle adapter is perfect ! - can you purchase from that guy ?
Regarding the Tubes, they must be precision, and 1 piece and as long as possible. We are testing wood to see if it works, we are wrapping laminate around it to cure, then pulling the laminate off, then re-using the mandrel, so it needs to be high quality uniform or slightly tapered surface finish so that laminate will slide off.
Regarding the CAD, what Im trying to do is a Mill - Turn operation. I know a lot of software can calculate this stuff automatically, but the biggest issue is things like - some software assumes the rotary axis is alligned with the X axis only. Is there a way to change the axis to have the rotary alligned with the Y axis ?
Basically need to be able to configure some software with stepcraft, with rotary paralel to y axis and so that it can to 3d Milling, then turn face 90 degrees, then 3d mill.
Any ideas?
I had another look at deskproto. By default it limits the rotational axis to be inline with the X axis. and removes the Y axis options. Is this software then setup only to do rotating milling operation, and not 3D operations, followed by a rotate, then another 3D?
I cannot find any video of this, it all seems to be rotate and mill or nothing?
- 44 Foren
- 7,333 Themen
- 63.2 K Beiträge
- 15 Online
- 26.3 K Mitglieder