Dear user, the forum software has been updated. For the first login please reset your password.
Dimensional problem on X/Y axes
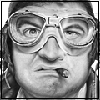
My little Stepcraft 420 consistently have a dimensional error along X and Y axis: it makes all parts 0.2 mm smaller (two tenths).
Yesterday I've made a test-session by milling some plates on a simple MDF plate using a 2mm end-mill that I regularly use for alu/plastic.
test 1: a rectangular shaped 53x48 mm plate with some circular holes of various diameter located near the four corners of the plate.
test 2: a rectangular shaped 100x100 mm plate with some circular holes of various diameter inside.
In both case the plates was around 0,2 mm smaller in X and Y dimensions (tolerance +/- 0.03 mm). 🙁
I immediately thought about a possible run-out problem at the spindle-collar, but... all the circular holes are almost perfect! (Maybe just an error around 0.003 mm - 3 cents of mm).
In case of run-out it should make all the parts smaller of 0.02 mm, isn't it?
As next step, I've double checked the generated G-code, but it seems simply perfect to me. Also the coordinates shown on the computer screen while machining the part are ok.
I'm going crazy with this problem. I cannot realize where the problem is. :unsure:
I also thought that my machine is loosing steps. But in this case I should observe a grater dimensional error when doubling the size of the plate (from test 1 to test 2 above). Isn't it?
I made my tests on MDF intentionally maintaining the same mill-bit, feed-rate, and DOC I'm using on ABS and POM plastic (dia = 2mm, feed = 400 mm/m, DOC = 0,5 mm). They seems pretty conservative to me.
I'm puzzled. Any idea? 🙁
SC300 + Spindle HF500 + Portalerhöhung + LinuxCNC + gsimple
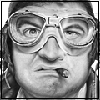
Additional Info.
I've shaken the portal in any direction. There is no evident play or backslash issue. The machine seems rock-solid on every axis.
As I remember, the machine is configured with 200 steps per revolution (original HF 500 Spindle from Stepcraft). The max acceleration should be around 30 mm/s^2
(I have to double check this values since the machine is not with me at home.)
SC300 + Spindle HF500 + Portalerhöhung + LinuxCNC + gsimple
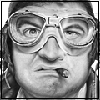
Hi Julius.
I had a similar problem in the past on another router machine.
I had slightly too harsh feed vs depth of path and the dimensional error was coming from tool deflection.
Have you tried the same test patterns with a slower feed?
++
Gael
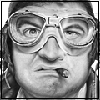
Hallo Gael,
I tried different feeds (adjusting RPMs) with the same results: that 0.2 mm error won't go away, while all the circular shapes are pretty good.
I wonder how tool deflection can occur on a soft material like MDF. I'm not pushing the device to his limits in anyway.
UPDATE:
today I decided to make a deep and serious test about backlash. The results have put me in profound depression... 🙁
SC300 + Spindle HF500 + Portalerhöhung + LinuxCNC + gsimple
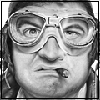
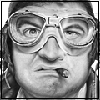
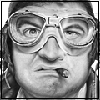
I'm quite disappointed from the machine. I've always machined soft plastic like POM or ABS, rarely I've machined alu sheets (max 1mm) and/or pipes (max 2mm of wall).
A backlash of 0.36mm is enormous in my opinion. I have big eyes.
Now I will try to apply the backlash compensation provided by LinuxCNC. Maybe it will help to minimize/reduce this problem, but I'm quite skeptic about a software solution.. we will see.
Anyway a mystery remains: why circular shapes have an error of just few cents? My hypothesis is what follows: since the circular pockets are made by a series of spiral movements along X and Y axis both, then there is a constant force that maintains the center of the spindle quite "stable". This is also because of the softness of the material and the modest deep-of-cut (0.5 mm).
SC300 + Spindle HF500 + Portalerhöhung + LinuxCNC + gsimple
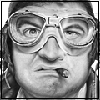
By the way, here a couple of well-made articles that helped me a lot in the comprehension of the backlash-problem:
http://www.machinetoolhelp.com/Repairing/What_is_backlash.html
https://www.imwsrv.com/cncmachwhat.pdf
About the right procedure for measuring the backlash, a simple goggle research produces tons of examples.
A note:
in my test I've placed a tiny sheet of rubber below/behind the caliper gauge to keep it firmly in position. The material is Viton, a really "sticky" rubber, but I think any rubber with medium/low hardness will work the same.
SC300 + Spindle HF500 + Portalerhöhung + LinuxCNC + gsimple
- 44 Foren
- 7,338 Themen
- 63.2 K Beiträge
- 4 Online
- 26.3 K Mitglieder